Gas Well Deliquification: Foam Assisted Lift (FAL) Part-II
- Imran Tayyab
- Sep 21, 2016
- 3 min read
In part-1 of our blog on FAL, we discussed the two types of foaming that is widely used in the industry, Soap Sticks & Capillary Foam Assisted Lift. We also went over the equipment typically used in CFAL setup. In this part of Foam Assisted Lift blog, we will discuss the considerations that should be focused while selecting a water producing well for Foam Assisted Lift. We will also cover the analytical modeling that is used to simulate wellbore hydraulics of a well installed with foaming technology. So without further ado, lets get right in!
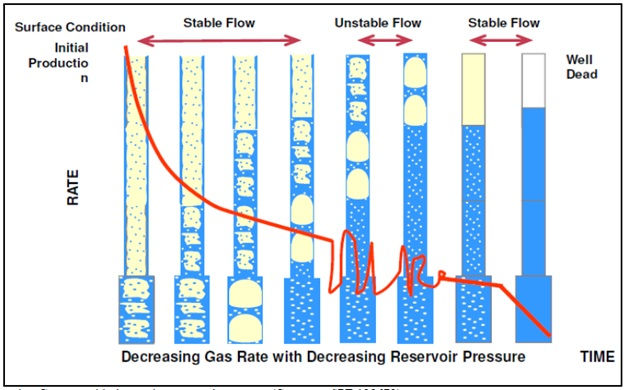
Excellent depiction of multiphase flow in wellbore as well moves towards liquid loading - SPE138672
Foam Assisted lift (FAL) is one of the gas well de-liquification methods used to remove water from the tubing and safeguard the well from liquid loading. The goal is to reduce the interfacial tension between the gas and the liquid and lessen the settled liquid density by injecting surfactant (commonly known as soap) resulting in smaller liquid droplets which are easier to carry since they have low critical velocity. This helps to dewater the wells at lower velocities and rates.
FAL Candidate Selection Criteria
Foam lift is comparatively simpler and has fewer foot prints; however there are some basic considerations which should be kept in mind before opting for foam assisted lift.
Water Rate: If the water rate is below 500-700 BPD and water cut is high i-e greater than 70% FAL could be applied to unload the well and extend well life. Water rates exceeding 1000 BPD are not suitable for FAL.
Single Liquid Phase: For FAL 100% Water is the best. More than 50% Oil/Condensate is difficult to foam. Normally, the wells with water cut above 70% are very good for this.
Gas Liquid Ratio: There is no upper limit of GLR. The higher the GLR, the lower is the operating cost.
Proper Foam Selection: Foam selection should be made based on bottom hole temperature and reservoir fluid nature. For temperature greater than 300 deg F, high temperature foamers must be used to add stability, compatibility testing is highly recommended between reservoir fluid and foam before injecting it in to the wellbore.
Foam Assisted Lift Analytical Model
Foaming is used in the industry for a while now, however interestingly research on modeling front for this niche technology has been in limbo. Only the latest version of industry standard PETEX IPM suite included an option that attempted to develop Vertical Lift Performance for wellbores that are completed with this technology.
The mechanics were outlined by Li et al (PETSOC 2007-118) which correlated the interfacial tension and densities of gas and liquid to calculate the critical gas velocity. Finally they substituted this critical gas velocity in rate equation to estimate flowrate in a known diameter cross section (tubulars). Following are the equations (taken from Li et al - Petsoc 2007-118):

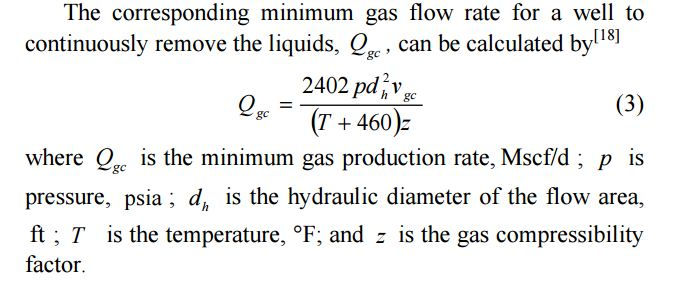
Although a novel take at modeling foaming in wellbores, we tested this model on several gas wells that are completed with foaming technologies and found that they were close at best in estimating gas rates. A major reason for this disagreement may be the default values of interfacial tension, a key parameter in calculating Vgc or critical gas velocity that we used. However in general, it will be remotely available for most operators. A funny dilemma, as specialized lab test is required to measure interfacial lab test and conducting such tests on a well that is marginal and requires foam lift will never make economic sense.
There is a significant potential for research in understanding the physics behind flow in a foam assisted lift well. In 2014, we undertook a project to develop a new artificial lift technology, called Foam Assisted Gas Lift (SPE-174525) that was a unique combination of gas lift and capillary foam assisted lift (CFAL) and proved to more efficient in optimizing, rates, reserves and economics than both its constituents’ technologies. We also collected extensive field data for application of that technology in pilot wells and using that data, we are currently working on an modified empirical model to simulate wellbore hydraulics under foam injection. This is an active research at ProPetra, and if you are interested (to learn more or join in the research), please reach us at research@propetra.com.
If you like this blog, kindly like and comment.
Comments