Fracturing Fluids Components: Introduction to Fluids and Additives used in Hydraulic Fracs
- Imran Tayyab
- Nov 24, 2016
- 2 min read
Hydraulic Fracturing has taken oil and gas industry by storm and its significance and usefulness especially in tight formations like shales and coal bed methane (CBM) is well known. Fracturing fluids are the most basic and vital component of fracking. Frac fluids are composed of variety of chemical additives such as gelling agents; guar (natural or synthetic), crosslinkers (titanium, Zirconium etc.), Clay control agents, friction reducers, surfactants, bactericides, pH control agents, fluid loss additives, breakers etc. All of these additives are added to formulate a frac fluid that must have adequate viscosity, friction control, formation-compatibility, and fluid-loss control etc. to perform the job designated to it – carry proppants to the fracture and flowback without damaging the formation.
Frac fluid selection is definitely one of the most important criteria to ensure successful frac job. An incompatible frac fluid would result in formation damage, excessive fluid leakoff, inadequate frac width and above all reduced capacity to carry (suspend) proppant for transport. If these qualities deteriorate to a greater extent, they will result in job failure, a screenout or extensive proppant pack conductivity damage.

Crosslinked frac fluid - Ref: hexionfracline
There are two types of frac fluids that have been used in the industry; conventional and unconventional.
Conventional Frac Fluids
These are mainly water based and hydrocarbons based fluids and are preferably used in sandstone and carbonates fracking in which formation permeability is not extremely low. They usually employ a gelling agent (natural or a derivative of guar gum), to create linear viscosity, a crosslinker agent that magnifies the viscosity exponentially through delayed action and a breaker system that diminished the viscosity of fluid to flow it back.
Unconventional Frac Fluids
The non-polymeric fluids, visco-elastic surfactants fluids, liquefied CO2 & N2 fluids (also known as Foam Fracturing) and, petroleum based fluids are often used in very tight gas formations where the initial water saturation in the reservoir is less than the capillary equilibrium irreducible water saturation. In such formations use of conventional water based fluids might cause water blockage in the near wellbore area and obstruct the gas flow path post frac.
Following on, we will focus on conventional frac fluids properties and additives for the purpose of this article.
As a rule of thumb, to get the job done, conventional frac fluids must have following properties:
It must have adequate viscosity ~400 cP at 170 s-1 shear rate for cross-linked fluid to transport proppants efficiently.
It must withstand the well’s bottom hole temperature during job pumping.
Added breakers should be able to break it down to low viscosity fluid once the pumping is finished and formation closure is achieved.
It should be compatible with formation rock and reservoir fluid.
Generate enough pressure drop along the fracture to create a wide fracture
Cost effective
Following table summarizes the different additives used to formulate a fracturing fluid.
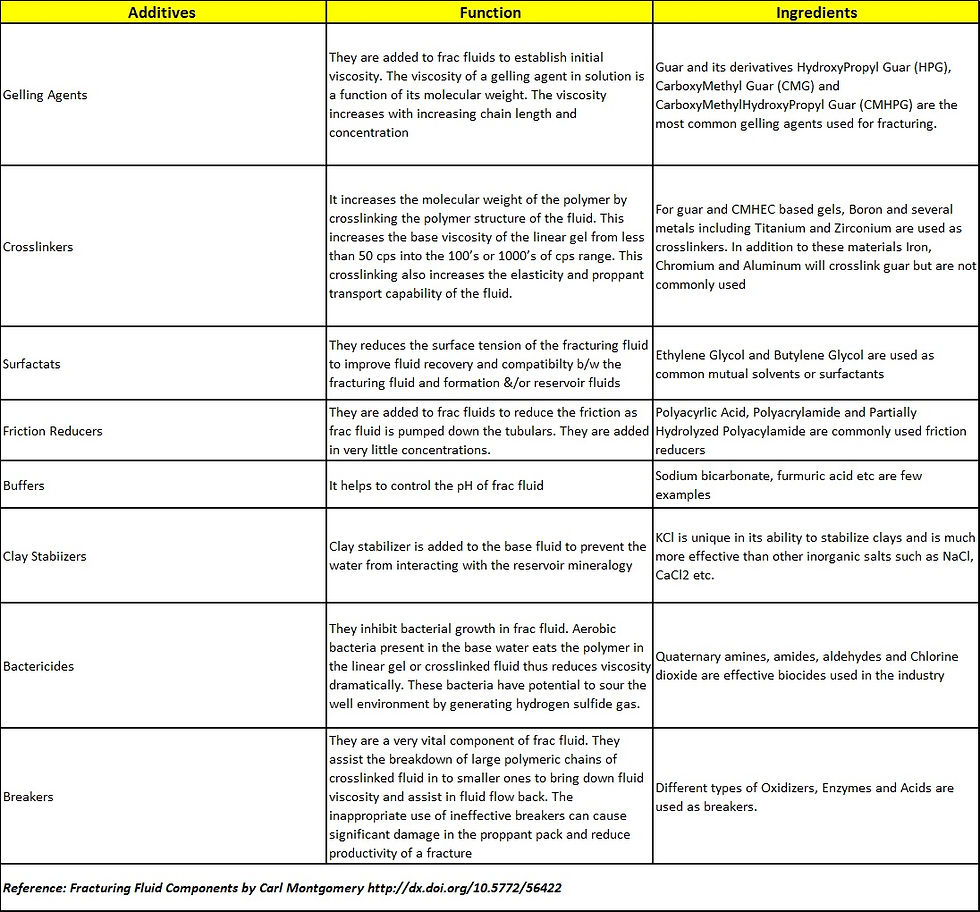
We hope this article was helpful in introducing the components of frac fluid. In the next iteration, we will focus on frac fluid testing, an important step in preparation of hydraulic frac job. Frac fluid reciepe is created and tested at reservoir conditions as per the design treatment schedule to evaluate the viscosity profile and ensure that fluid will perform as required.
If you like this blog, kindly comment and share.
Kommentare